News
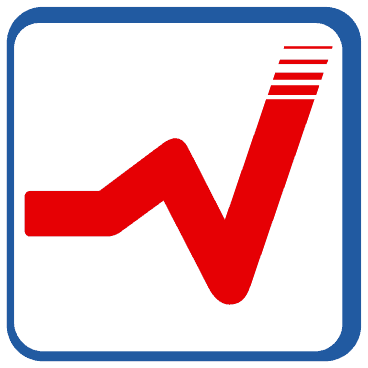
US Digital will be co-exhibiting with Angst+Pfister at Sensor+Test 2024 in Nuremberg, Germany. Read More »
Published 4/1/2024 in News > Events
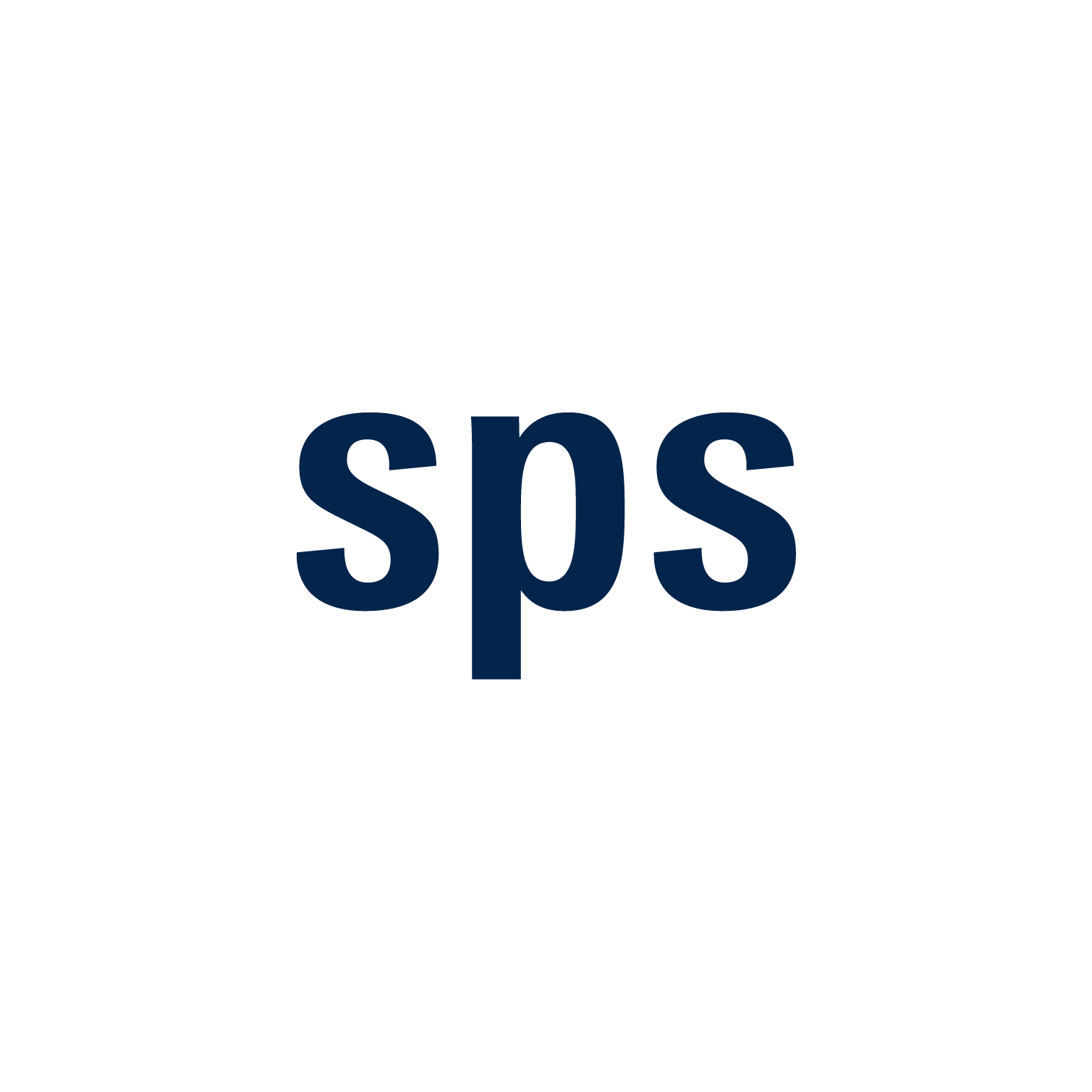
US Digital will be exhibiting in booth 1-628 on November 14 - 16, 2023 at SPS - Smart Production Solutions Event located at NürnbergMesse, in Nuremberg, Germany. Read More »
Published 9/25/2023 in News > Events
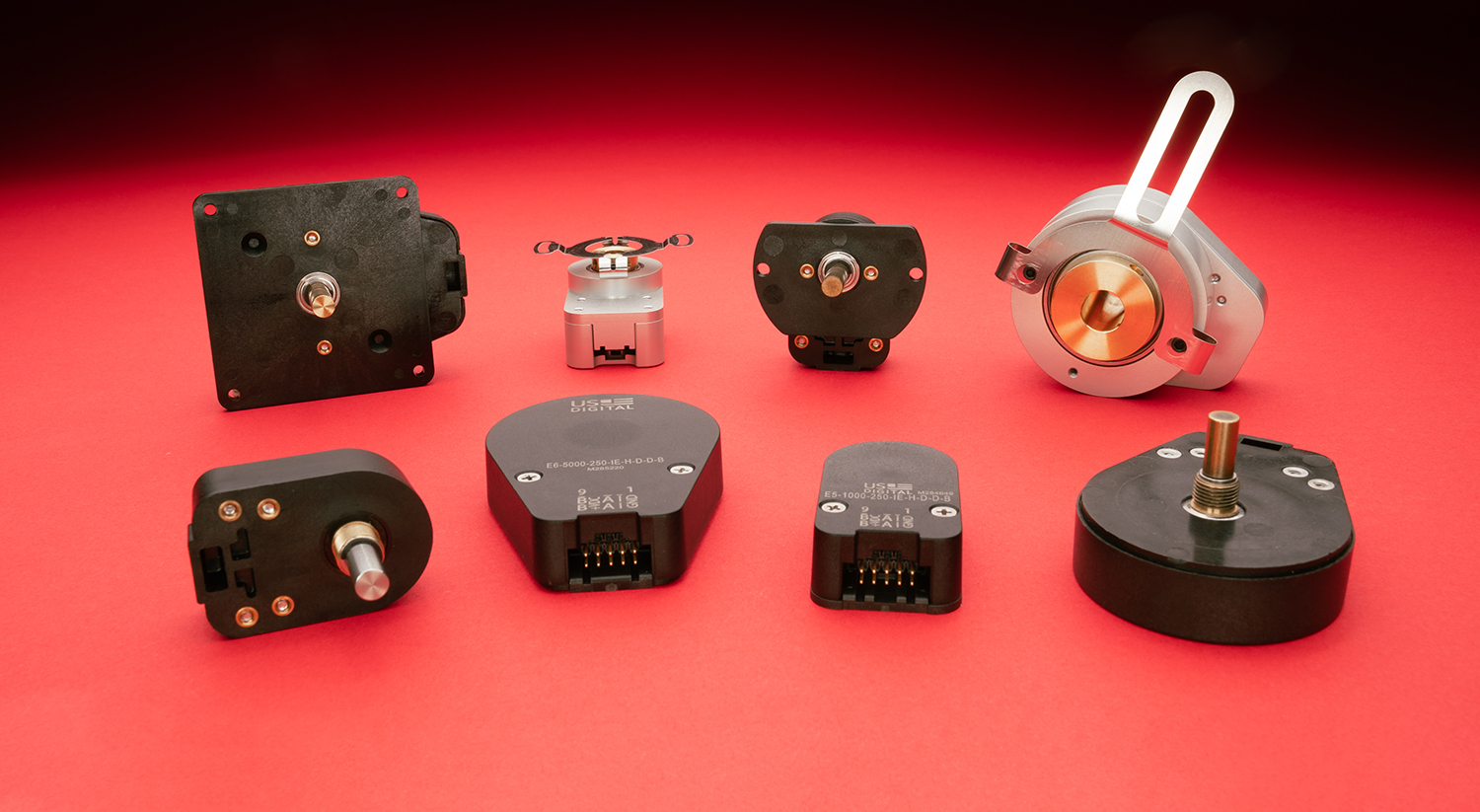
US Digital is announcing a new output configuration that enables many of its popular incremental encoders to accept power up to 30VDC without external adapters. Read More »
Published 9/20/2023 in News > Press Releases
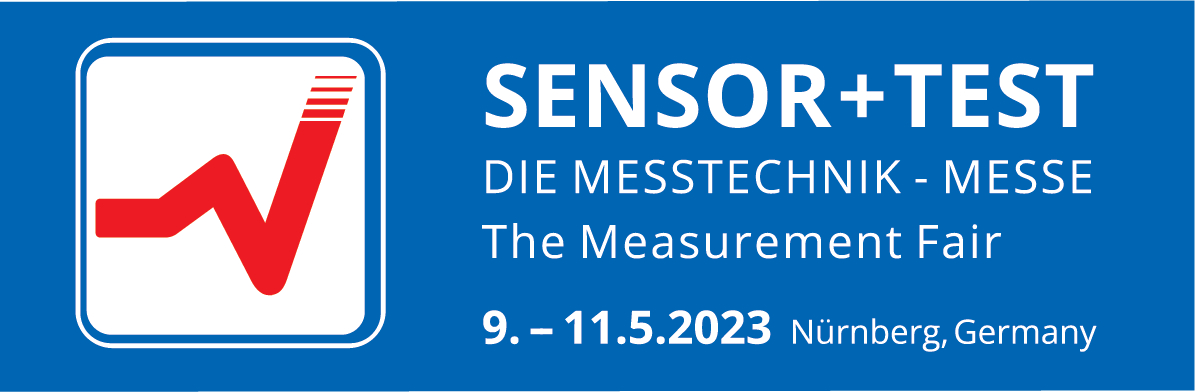
US Digital will be co-exhibiting with Angst+Pfister at Sensor+Test 2023 in Nuremberg, Germany. Read More »
Published 3/15/2023 in News > Events
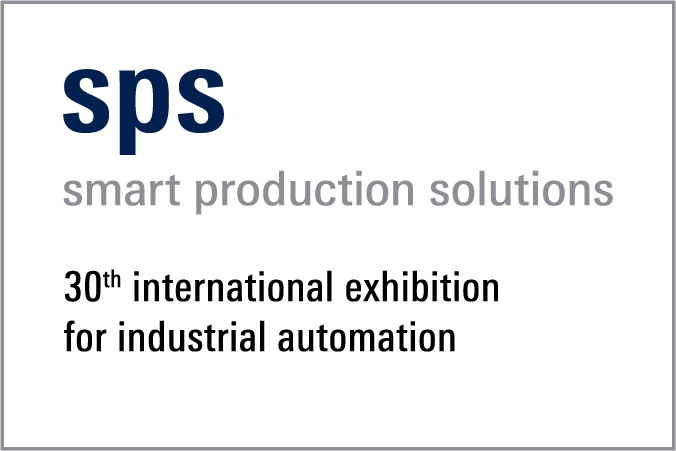
US Digital is excited to be returning to Germany and will be exhibiting in booth 1-100 on November 8 - 10, 22022, at the 31st Annual SPS - Smart Production Solutions Event located at NürnbergMesse, in Nuremberg, Germany. Read More »
Published 9/27/2022 in News > Events
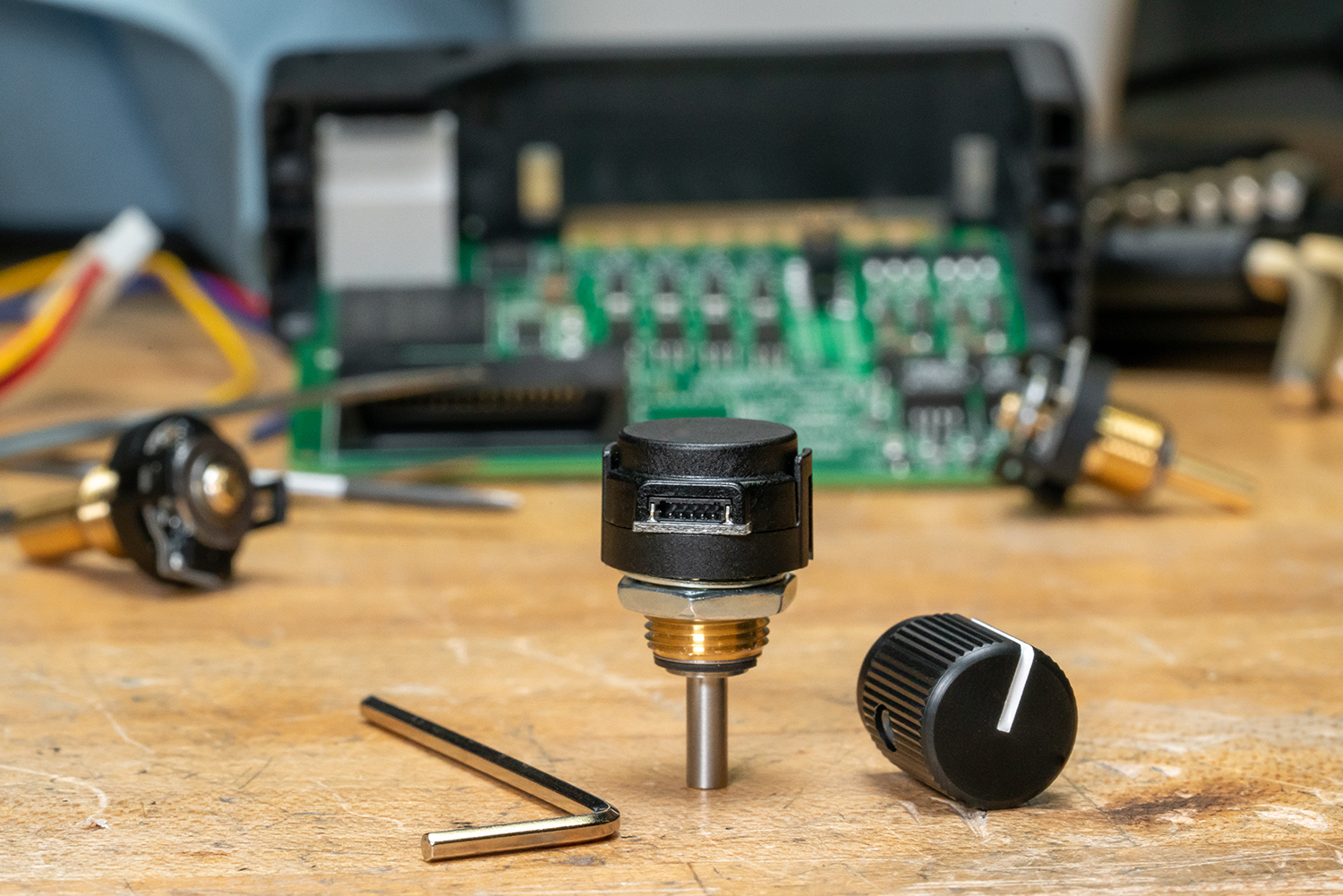
US Digital on January 17, 2022, announced it was expanding its line of miniature encoders with a new shafted encoder, the S16. Read More »
Published 1/18/2022 in News > Press Releases
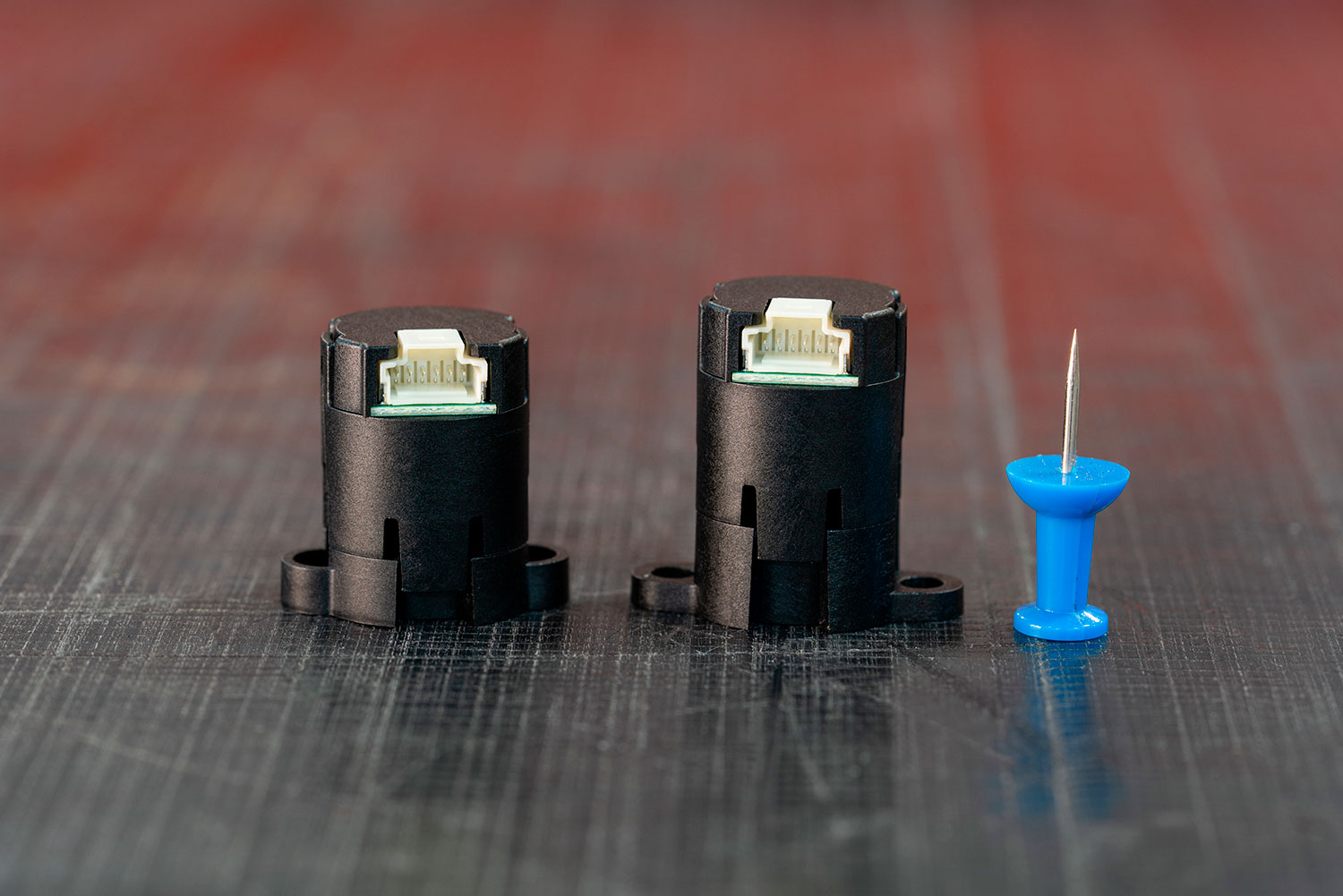
The new M3K Miniature Magnetic Encoder is available with incremental output or an incremental and 12-bit absolute output configuration. Read More »
Published 2/21/2021 in News > Press Releases
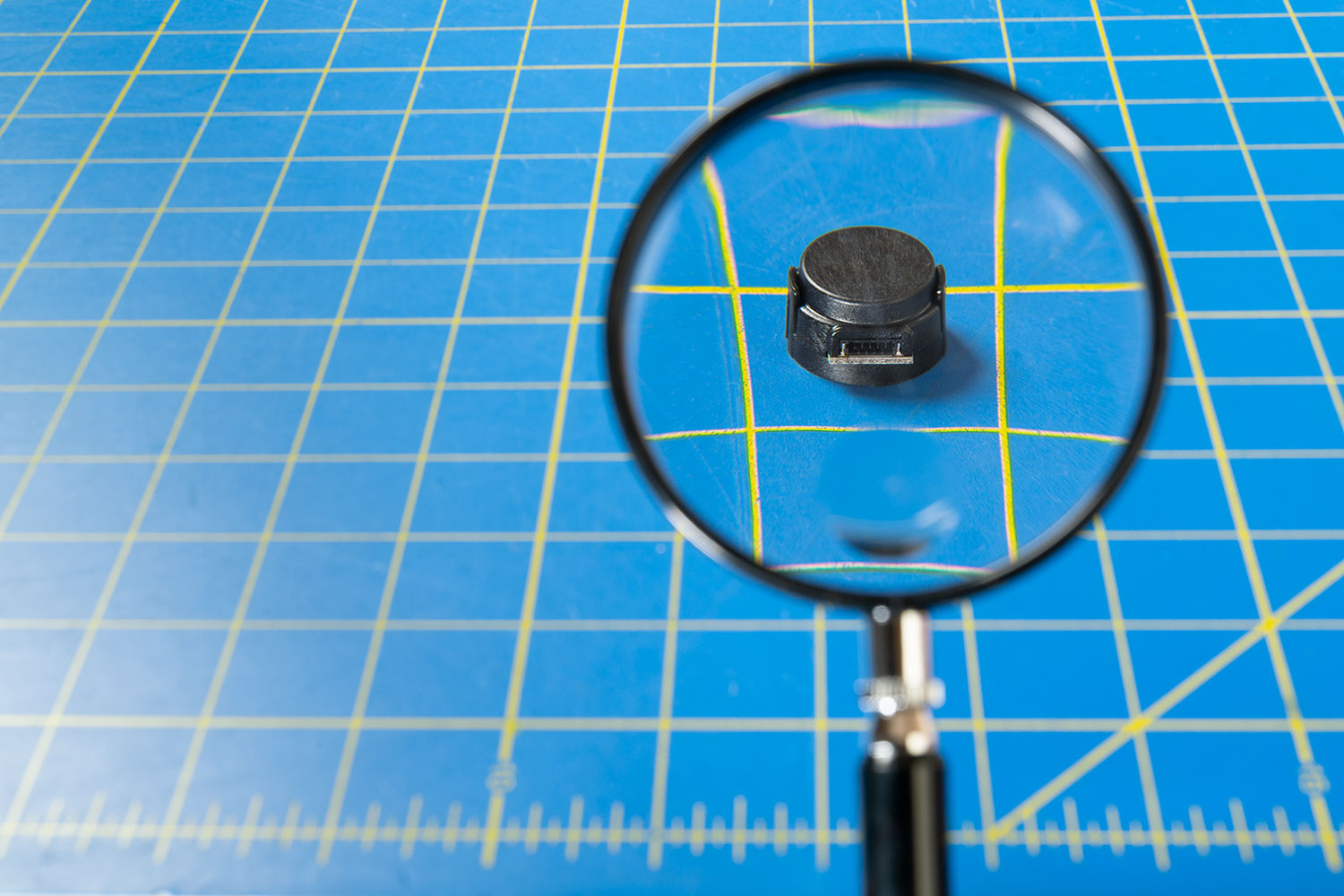
The new E16 Micro Optical Kit Encoder has a 10mm bolt circle, fits 1.5mm (0.059″) and 2mm (0.079″) shafts and provides A, B and Index digital quadrature signals. It comes in a variety of resolutions ranging from 250/256 to 4,000/4,096 CPR. Read More »
Published 9/16/2020 in News > Press Releases
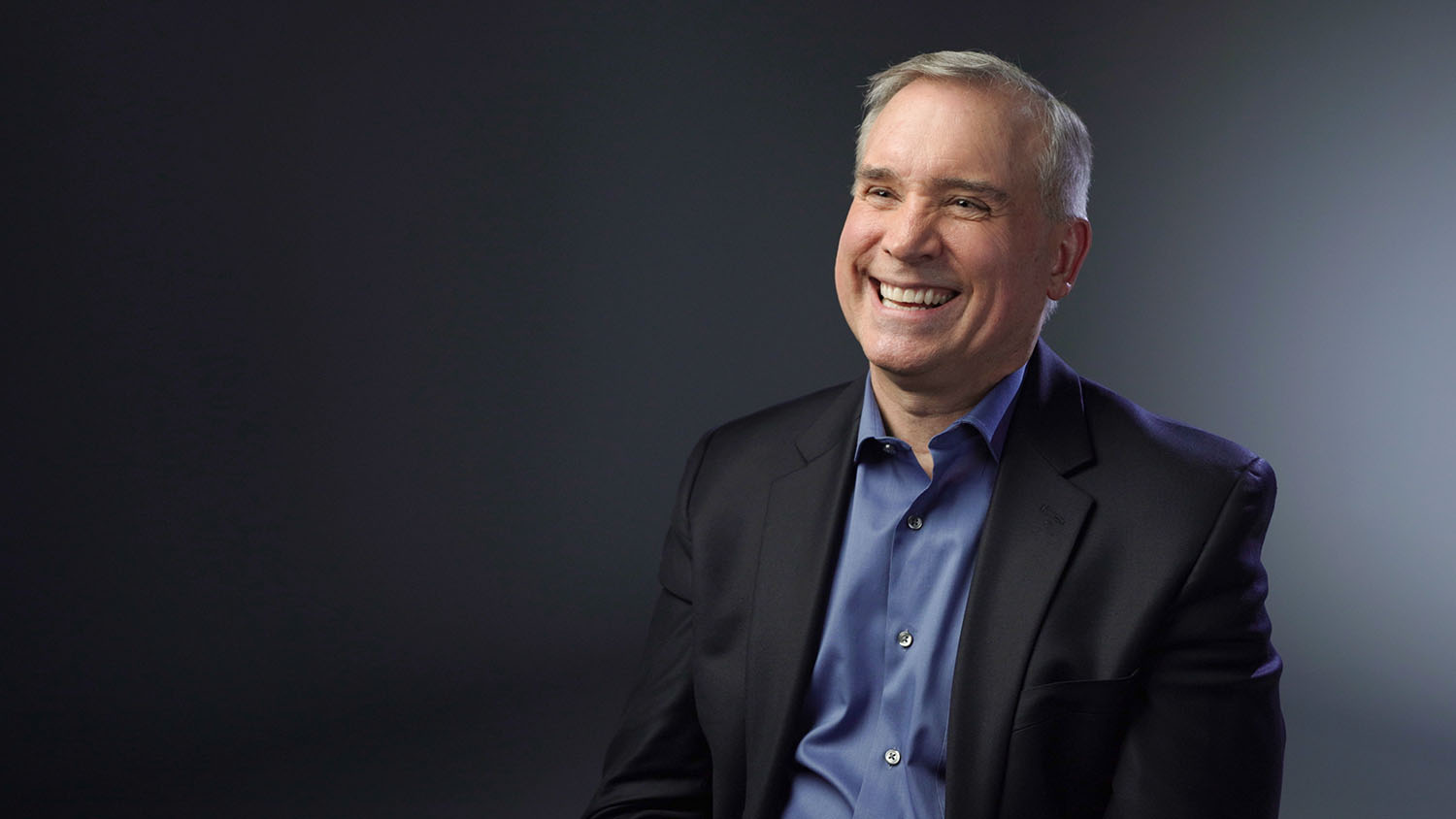
US Digital in May celebrated its 40th anniversary as a U.S. Manufacturer of optical encoders and other motion control components. Read More »
Published 5/26/2020 in News > Press Releases
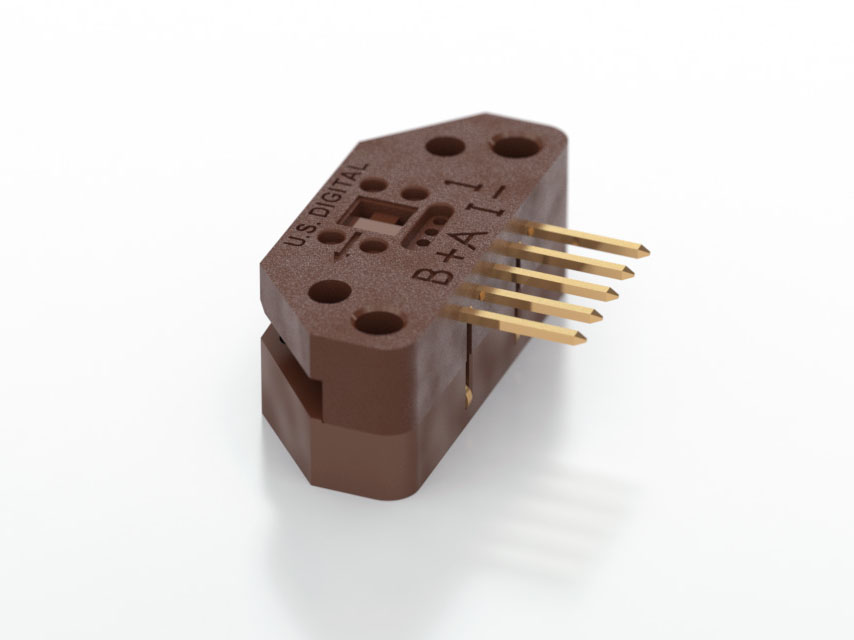
US Digital on Tuesday announced that it is adding 800 CPR resolution to its EM1 transmissive optical encoder. Read More »
Published 3/18/2020 in News > Press Releases
More in News
Stay up to date
Sign up for our newsletter to stay up to date with our product updates, blog posts, videos and white papers.